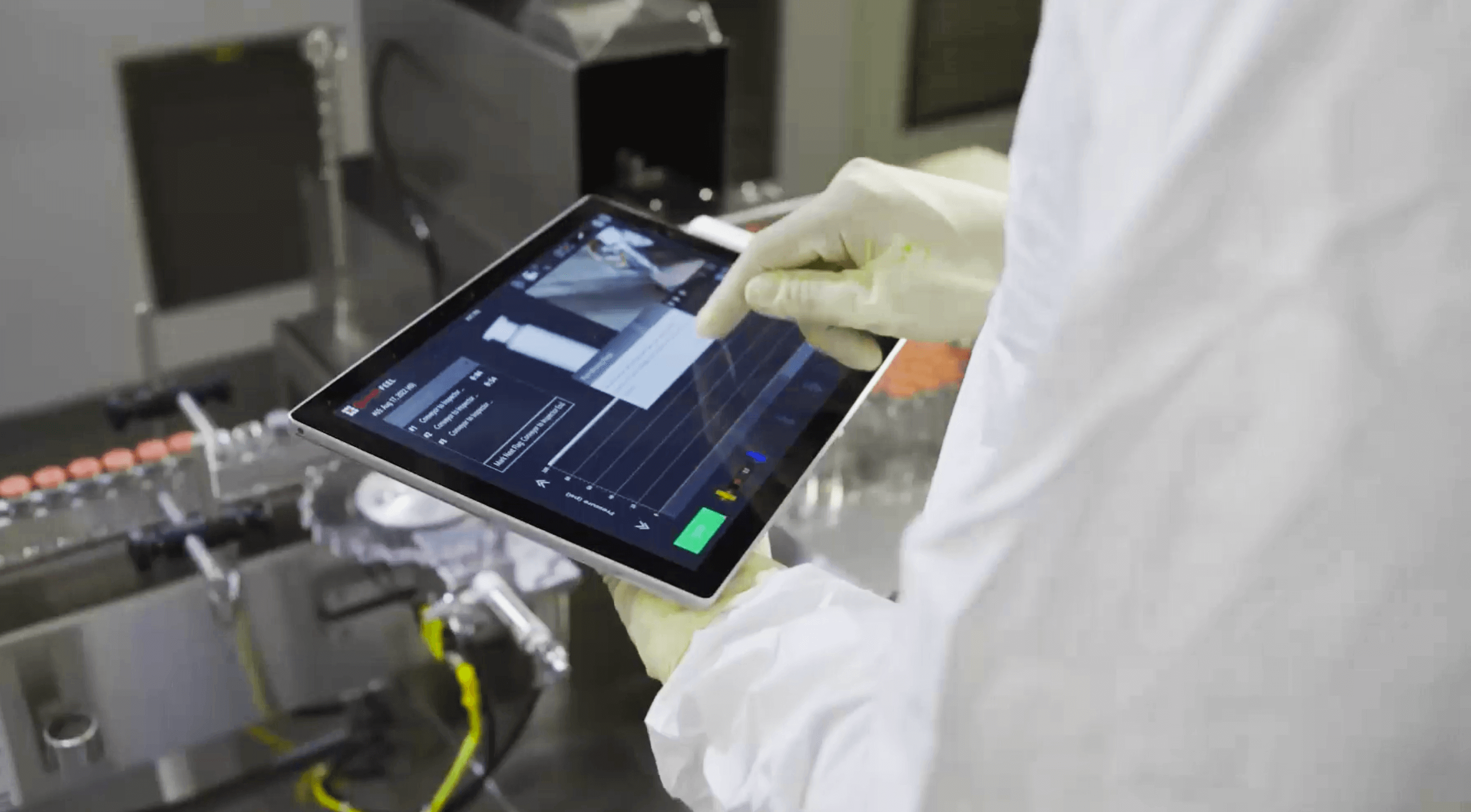
SmartSkin, an investment that pays for itself
In high-speed manufacturing, efficiency is paramount. Whether you’re producing beverages in aluminum, glass, or PET, or aseptic pharmaceutical products, every second of downtime and every defective container translates directly into wasted product, lost revenue, and rising costs.
SmartSkin is more than just a quality control tool—it’s a strategic investment in efficiency, waste reduction, and profitability. In this blog, we’ll explore how beverage and pharmaceutical plants can harness SmartSkin to drive operational excellence and generate ROI that pays for itself.
1. Minimizing downtime while maintaining optimal line speeds
Every minute your production line isn’t running at full speed, you’re losing money. In the beverage industry, this downtime can lead to high scrap rates, while in pharmaceutical production, it may increase contamination risks and trigger costly revalidation processes. Simply put—the longer it takes to detect and resolve an issue, the higher the losses. SmartSkin’s real-time analytics platform enables maintenance teams to quickly pinpoint the root cause of line issues instantly, allowing for rapid corrective action. By running the system at full line speed, you gain instant insights into where excessive pressure, rotation, or tilt is occurring along the line. This data can be easily analysed to identify recurring problem areas along the line. With rapid feedback, adjustments can be made and validated by rerunning the system, enabling efficient and streamlined troubleshooting.
With SmartSkin you get:
- Reduced time spent troubleshooting operational inefficiencies: Container twins that are replicas of your container can run along the packaging lines at various speeds to help quickly identify points where pressure is occurring in order to make necessary adjustments.
- Faster ramp-up speeds after a package or product changeover: If issues occur after changeover, SmartSkin can diagnose where on the line they are occurring within minutes.
- Consistent quality control for operational efficiency: SmartSkin’s container twins can be deployed on operating lines at high speeds to identify areas where these speeds could potentially affect product quality. Running the SmartSkin container twins frequently on the line after changeovers, adjustments to equipment, or at different speeds can help ensure that no further damage will occur allowing for optimized production.
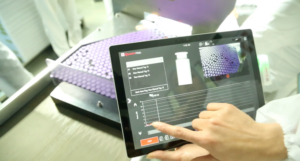
The SmartSkin software providing real time data
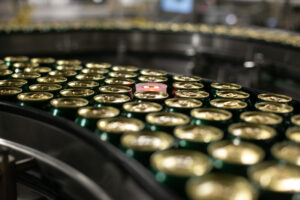
SmartSkin container twin on the a can line
2. Reducing the occurrence of rejects and protecting product integrity.
In the beverage industry, container defects lead to reduced total yields, wasted product and a strain to brand reputation while for pharmaceutical manufacturing, issues on the line can lead to unstable fill weights, high reject rates and compromised packaging integrity. With SmartSkin, you can maintain smooth product handling through:
- Rapid identification of high rejects which reduces waste from underfilled products or improper sealing processes. Being able to go through almost all areas of the fill finish process in both pharma and beverage plants allows for robust data to assess the conditions of the lines and make precise adjustments.
- Real-time insights enable maintenance teams to resolve issues in minutes, not hours, with the added benefit of rerunning container twins after implemented adjustments to verify that the issues have been resolved before resuming operations.
- Reduced scrap rates from damage, leakers, and misaligned packaging.
- Validating equipment set up to ensure compliance with regulatory standards in both pharmaceutical and beverage plants.
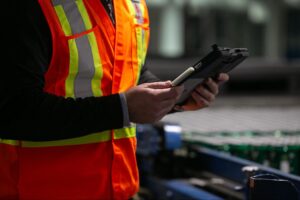
Beverage plant worker observing SmartSkin software
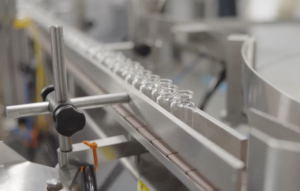
Pharmaceutical vials on the line
3. Improved audit performance
For pharmaceutical manufacturers, service requests often lead to delays in validation and compliance—particularly when regulatory bodies like the FDA or EMA require precise reporting on packaging integrity. In beverage and food processing, frequent technician visits drive up operational expenses and contribute to lost production time.
Equipping in-house teams with SmartSkin’s diagnostic tools eliminates the need for costly third-party troubleshooting and repetitive audit requests. With proactive monitoring, companies can perform preventative maintenance and avoid catastrophic failures.
Final Thoughts
In high-speed beverage and pharmaceutical manufacturing, efficiency isn’t optional—it’s the key to profitability. SmartSkin doesn’t just enhance quality control; it actively reduces costs by minimizing downtime, preventing waste, and improving audit performance.
By leveraging SmartSkin’s real-time diagnostics, manufacturers can:
- Maximize production efficiency with faster changeovers and optimized speeds
- Minimize waste by identifying and correcting issues before they impact output
- Resolve problems faster with real-time data-driven insights
- Ensure regulatory compliance while reducing reliance on external auditors
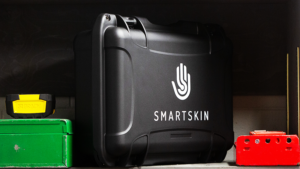
The SmartSkin System
The bottom line? SmartSkin isn’t an expense —it’s an investment that saves costs. Want to know how much your plant could benefit? Contact us today for a personalized cost-benefit analysis and see the ROI firsthand .