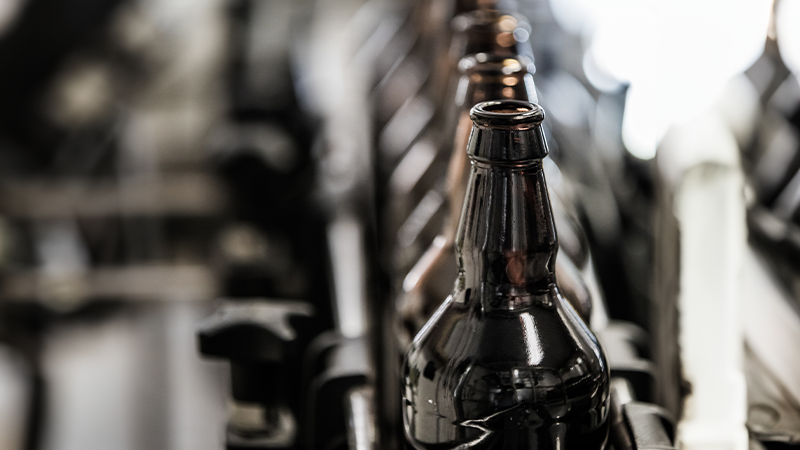
Understanding Glass Damage in Beverage Manufacturing
Assessing the Impacts of Glass Damage
The demand for bottled beverages remains high globally, putting pressure on manufacturers to maintain a consistent output of high-quality products. This challenge is particularly acute with glass bottles due to their inherent fragility. Unlike other materials, damage to glass not only leads to financial losses, product waste, and operational delays but also poses serious safety risks to consumers. Even the smallest defect in a glass bottle can jeopardize consumer safety, making it essential for manufacturers to understand the causes of glass damage and swiftly address any issues. This is vital not only for operational efficiency but also for ensuring public health and safety.
Identifying Glass Damage
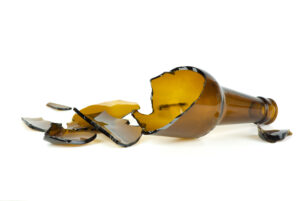
Shattered brown beer bottle
While most people think of “glass breakage” as a bottle cracking or shattering, other, less obvious forms of damage are equally important to monitor. These include:
- Scuffing/Scratches – Minor abrasions that may compromise bottle integrity.
- Cracks – Leading to product spillage or weakening of the glass structure.
- Micro-breakage – Small fractures visible only at a microscope level but are still dangerous.
- Glass Breakage – Obvious and hazardous breakage.
- Glass Explosion – The most severe form of damage, posing immediate safety risks.
Since glass bottles are often reused in bottling plants, they become increasingly susceptible to wear and tear, further elevating the risk of breakage over time. Proper line setup and maintenance are crucial to minimize these risks.
Common Causes of Damage
The graphic below shows common areas on the line where glass damage may occur.
As shown, glass damage can occur at almost any point along the production line, but the most critical zones are typically:
-
Washer exit
-
Packer infeed
-
Pasteurizer
Achieving operational efficiency requires managing key parameters: pressure, speed, temperature, and lubrication.
- Pressure: High-pressure readings can signal issues like misaligned guide rails, worn or damaged equipment, or incorrect conveyor curves. These lead to improper product flow and increase the risk of damage.
- Speed: Faster line speeds can increase production yields, but if speeds aren’t synchronized across the line, damage becomes more likely.
- Temperature: Glass is highly sensitive to temperature fluctuations. Zones such as the washer and pasteurizer, where temperatures vary, are particularly prone to damage if not properly regulated.
- Lubrication: Insufficient lubrication increases the chances of impact damage, while too much lubrication can speed up the line and lead to unintentional impacts.
Preventative Measures and Troubleshooting
Even if after monitoring the parameters above, glass damage persists assessing the following areas may help in identifying the root cause:
- Worm, starwheel, and infeed timing:
- Machine setup clearances and rail clearances:
- Conveyor speeds and lubrication
- Pressure and shock minimization during filling and conveyance
- Worn or damaged conveyor rails
- Palletizer layer clamping forces
- Pallet quality and warehouse handling practices Forklift operations from moving pallets from warehouses to trucks as well as the movement between warehouses and across great distances.
Key Takeaways
Bottling facilities will no doubt retain their product of beverages using glass for a number of reasons such as cheaper access to raw materials, warmer climates where glass beverages fare better at remaining cool, sustainability advantages of glass being reusable and most importantly- a persistent culture that will continue to enjoy beverages in the glass form.
In today’s day and age, there are many processes already in place that ensure consumer safety with glass beverages. As will any material, the responsibility lies in the manufacturing team to work together to ensure that each step in place (at all levels) is accounted for, and the necessary preventative as well as diagnostic measures are well understood across the facility. This is of utmost importance as the fragility of glass makes a very volatile substance and the consequences of its damage pose exponentially higher stakes to its consumers.