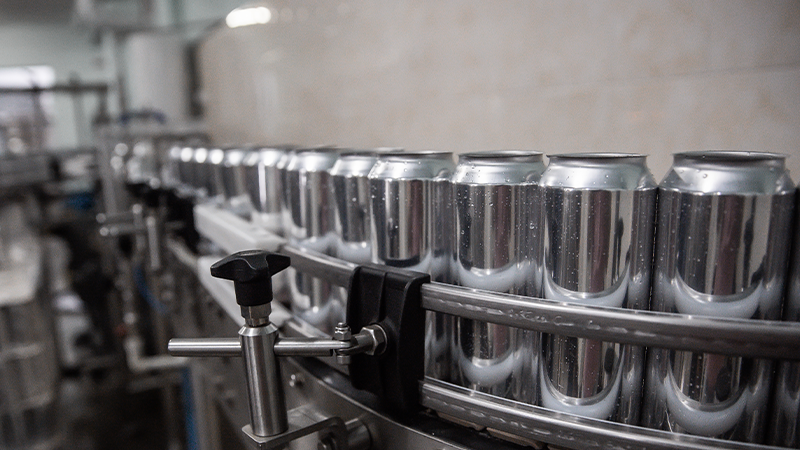
Beverage Can Damage – where does it come from?
Most of us in the beverage industry are also consumers, and seeing damaged cans for sale on shelves is not a great representation of the quality of the cans and beverage filling operations. For many years, steel food cans that were dented were believed to be spoiled and then left behind on the shelf by shoppers. Beverage can damage, in its worst form, leads to the inner lining being disrupted and being weakened, giving the beverage and its ingredients the opportunity to escape as a leaker in warehousing or on store shelves. These leakers can be accelerated with warmer temperatures and with some of the concentrated flavoring and ingredients used in the formulas today.
The can converting plant – damage Origins.
Modern aluminum beverage cans are made and decorated at high speeds (more than 2000 cans per minute per line). They begin life as a roll of aluminum, are punched into silver bodies and then after decoration, spin necking and flanging, become a finished can. They are bulk palletized for warehousing and shipment to the beverage filling plant.
These operational steps are the first place where can damage can occur, on an individual can line in the form of dents, and then in warehousing and transport operations. Pallets can be damaged in truck loading or unloading and warehouse storage. When these are delivered for use, the palletizer operator might pull out some damaged cans, but some may get through to the filler.
Shoulder dents
These storage and handling practices are a first place to start to improve the quality of can deliveries to the bottler plant.
The Filling plant – damage can accelerate
Bottlers must respect the pallet quality of cans and not contribute more damage through internal handling and delivery to the line. Once loaded on the line, the layers of cans are swept onto conveyors for transport to the filler. This is the next place damage can occur, as the can body is soft and flexible and can be pinched by conveyor pressure and single filing, and in the transport to the filler.
The filler and seamer together is a high speed environment where cans are redirected into filling platforms on rotary fillers and sealed and filled with beverage and then discharged to a seamer for end application. The can transitions from being a soft body to having an axial load, to a seamer with top load and exits with pressure building inside due to carbonation of liquid nitrogen injection.

Large wrinkles from filler worm
The timing of the star wheels and feeding screws are critical to handle the can carefully and not crease or dent the can body. If the can sees this damage, the wrinkle can be enhanced by Topload in the seamer. The seamer discharge is also a star wheel and the cans are accelerated against a guide rail to direct them to flex top conveyors. These rail contacts can also dent the can, even though pressure is building inside the can due to the beverage, it is still soft.
The next step in the cans journey is through a warmer or pasteurizer, fill level detection and then on mass conveyors to packers which create the multipack or market format of the cans. The cans are moved at 1200-1500 per minute, so these conveyors must produce a horizontal force to push them to the next operation. The forces on cans here can be a combination of conveyors motor speed, rail geometry and conveyor lubricant applied. If a packer stops, modern conveyors should slow down, stop and restart. When conditions are not right, cans moving in this area can have horizontal rail marks when high pressure pushes them against guide rails and heel or shoulder dents. The more time spent on the line, the more opportunities there are for damage.
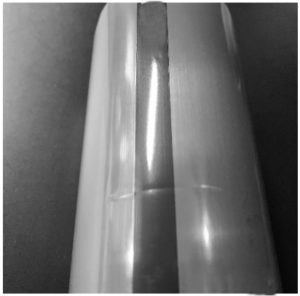
Rail Marks
The packing operation is where the multipacks or tray shrink packs of cans are created. Multiple lanes direct the cans inside paperboard wraps which are glued together and then sent to palletizers. These are the final steps where cans can be dented, but when inside a multipack, no one sees them until purchased. Can packs are palletized on wooden or plastic pallets. Nails protruding from wooden pallets are the last culprit to cause punctures and leaks.
What’s the impact?
Damaged or leaking cans can begin in the filling plant or weeks later in regional warehousing. Multipacks become wet with sugary liquid and this accelerates can corrosion from the bottom rim. In some cases, bottlers try and sort out damaged cans and remake good packages, but this takes labor and time and new multipacks which can cost $0.17 each per 12 pack. At the end of the day, with transport costs to consolidate bad cans, labor, and new packaging, this is an expensive operation which could have been prevented.
Joe Norris
New Product Development and Technical Service
Joe Norris boasts a stellar career spanning over four decades in the packaging and product development arena. Serving for ten years at SmartSkin Technologies in Fredericton, Canada, he’s an expert in New Product Development and Technical Service. Prior to this, Joe held pivotal roles at The Coca-Cola Company, both as Principal Engineer for Global Packaging R&D in the Greater Atlanta Area and earlier as a Packaging Engineer in Atlanta and London. His keen insights have influenced early concept ideation, design, and alpha engineering, with a particular emphasis on the commercialization of North American aluminum bottles and their resealable closures.
Joe’s journey also includes an impressive 15-year tenure at Colgate Palmolive Co in New York City and Piscataway, New Jersey. Initially, he championed package engineering leadership for top US brands, notably playing a key role in the successful launch of Total toothpaste in 1997. Later, he spearheaded a team advancing global brand and package technology innovation, securing the Global Technology Award in 2001 for dual tube commercialization.
A testament to his innovative spirit, Joe has an impressive portfolio of 18 issued patents with both Colgate-Palmolive and The Coca-Cola Company. His remarkable contributions to the industry underline his expertise and commitment to packaging and product development.