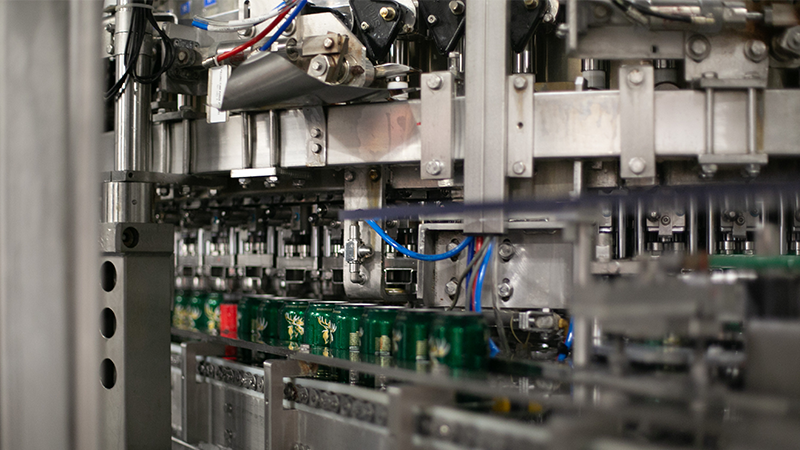
Suggested Seamer Preventative Maintenance Checks
Every equipment manufacturer should have available preventative maintenance manuals or guidelines upon request specific to their equipment. These suggestions are not intended to replace the original equipment manufacturer requirements but are intended to give generic guidelines for preventative maintenance on can seamers. All pictures and illustrations depicted here are from an Angelus seamer.
Daily Checks
- Check all oil and grease reservoirs and maintain levels with manufacturer’s recommended lubricants.
- If the seamer is equipped with an oil filtration, re-circulation system, check the pressures at the filter cannisters to be in manufacturer’s specification and visually check the color of the oil in the reservoir for contamination. Drain and refill if necessary.
- Grease all manual grease fittings on the seamer with the manufacturer’s recommended grease at the manufacturer’s intervals.
- Visually check the seaming chucks and rolls for cracks or chips. Replace any damaged chucks or rolls.
- Visually check the cover feed separator disc or discs for chips or damage. Replace the disc if damaged.
- Visually check for scrap materials in the can or end paths and remove any scrap material.
- Check can feed table and seamer can lifter plates for aluminum oxide build up. Clean off excess aluminum oxide with nonabrasive soap and nonabrasive pad. Check lubricant flow and consistency on wear plates.
- Jog a Smart Skin Pro Seam through the filler and seamer and review data if your company has one available.
- Check finish double seam dimensions internally and externally to be in factory specifications. Make adjustments accordingly.
Weekly Checks:
- Run a first operation seam check and check external dimensions to be in factory specification. Make adjustments accordingly.
- Check all can wear plate transfers from filler to can feed table and can feed table to lower chuck can lifting plates.
- Check for proper transitions on can guide transfers to be at proper settings.
- Using an aluminum pry bar depress vertically downward on the lower chuck can lifting plate to verify there are no broken springs or binding.
Monthly Checks:
- Check seamer can feed chain for damage, stretching or bent fingers.
- With seamer set up tooling (spindle plug) alignment of gassing turret to seaming turret.
- Follow through with checking proper clearance between seamer feed chain finger to spindle plug where the cover is inline with the top of the can. Some seamers were designed to be at 85°and some seamers were designed to be at 90°.
- Check general timing through discharge turret and discharge conveyor.
Yearly Checks:
- Change oil every 2,000 – 5,000 hours depending on oil manufacturers recommendation.
- Schedule time for a complete machine audit.
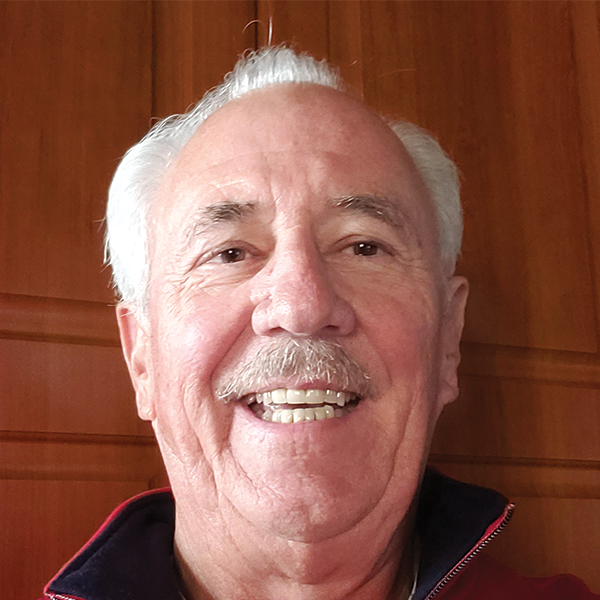
Kevin Wright
With an illustrious career, Kevin formerly held the position of Director of Customer Service for Angelus, where he was instrumental in providing technical support to both domestic and international field service representatives. His extensive expertise also saw him assisting the can reps and customer maintenance teams, cementing his position as a trusted and reliable figure in the field.
His vast experience isn’t just confined to Angelus. Kevin stands out as a global authority in seamer troubleshooting. His hands-on work with the SmartSkin solution in numerous Coca-Cola plants worldwide further testifies to his profound knowledge and skill set.