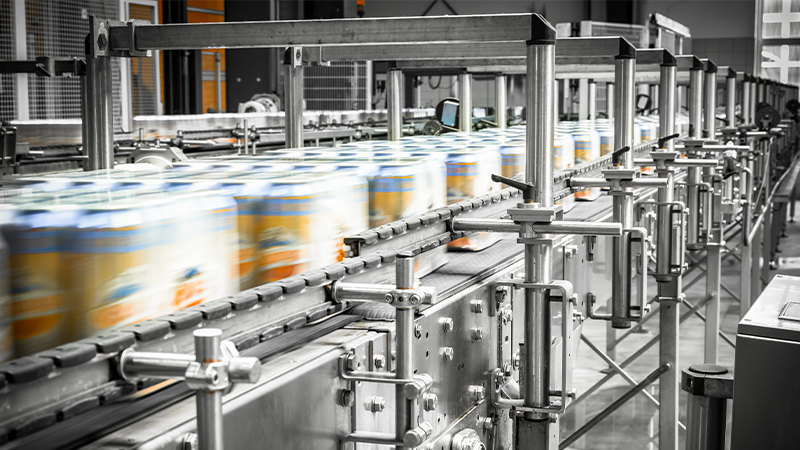
Identifying Common Forms of Aluminum Can Damage in Beverage Manufacturing
Assessing the Impacts
Beverage manufacturing facilities constantly strive to maintain high yields and product quality, despite the frequent occurrence of defects in aluminum cans. Damage to these cans can lead to leakers, affect brand reputation, and cause significant disruptions, as production stoppages often coincide with product loss, putting immense strain on operational efficiency. The repercussions of can damage extend beyond the production line—spoiled products that are shipped across cities or countries result in wasted time and resources for all parties involved, often only discovered too late.
Understanding the factors that lead to can damage, the various forms it takes, and the strategies to swiftly identify and address these issues is essential for ensuring smooth operations.
Common areas of Damage
The graphic below highlights the common points along the beverage filling line where aluminum can damage is typically observed.
While the severity of aluminum can damage varies, effective corrective actions should address all levels to maintain operational flow. Even minor initial damage can escalate into leakers if aggravating factors are not managed. Some of these factors include:
- Line speed: Increased speed can heighten can-to-can pressure and shock, potentially causing damage.
- Damage progression: Initial damage may compromise a can’s inner lining, leading to leaks during distribution or on store shelves.
- Leak propagation: A single leaker can cause adjacent cans to be coated with the beverage, resulting in multiple leakers.
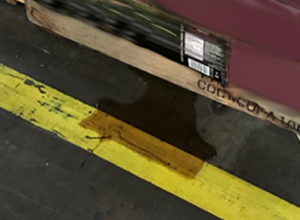
Both images show examples of spillage due to warehouse mishandling
Defect Categories
Let’s delve deeper into the levels of can damage and their severity. These categorizations are industry-standard terms used across manufacturing plants to describe various forms of damage.
Class I Defects: These are aesthetic and minor defects, serving as early indicators of more serious issues. If observed, line operators should adjust the process accordingly. Class I defects typically include dents, creases, scratches, and wrinkles less than 1.5 inches in size, usually found on the heel, shoulder, or neck pleats.
Class II Defects: Considered major defects, these require more significant corrective actions to prevent leakers, which may emerge days after the damage is visible, severely impacting quality scores. Class II defects include dents and creases over 1.5 inches, more than five dents, or cumulative dents exceeding 2.5 inches, and wrinkles larger than 1.5 inches on the body of the can.
Class III Defects: These are critical, high-risk defects that can impair the functionality of cans, especially during the high-speed processes. They increase the risk of fill tech rejects and must be addressed immediately. Class III defects often result from improper machine setup or pre-existing issues with cans supplied to the facility. They include short or wrinkled flanges, fractured domes, pinholes, neck pleats, and wrinkles of 2.5 inches or more.
Preventative measures and Troubleshooting
If damage is progressing through the classes and no corrective measures have been taken, consider investigating the following areas to identify the root cause:
- Worm, starwheel, and infeed timing: Especially for empty cans entering the filler.
- Machine setup clearances and rail clearances: Especially in the seamer
- Conveyor speeds and lubrication
- Pressure and shock minimization during filling and conveyance
- Post-filling twists: Consider eliminating twists from the line.
- Worn or damaged conveyor rails
- Palletizer layer clamping forces
- Pallet quality
- Training to warehouse workers to refine handling practices: More training for warehouse workers may be needed.
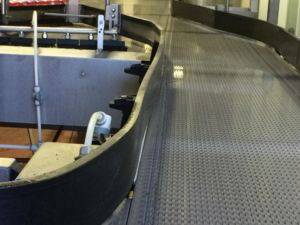
This image shows an example of bowed rails that may heighten pressure between cans
Takeaways
Aluminum can filling is a dynamic process, where today’s solutions might need to be revisited tomorrow. To maintain manufacturing efficiency, quick identification and immediate action are crucial. Moreover, documenting incidents and establishing clear processes ensures that all team members understand the necessary steps when damage occurs, leading to faster response times in the future.
Ultimately, facilities must maintain a high level of vigilance and responsibility at all levels, as the challenge of recognizing, understanding, and addressing can damage is ongoing. While there’s no one-size-fits-all solution, a collective commitment to vigilance can help overcome this daily battle.